Corrélation d’images numériques (DIC)
Nous proposons une solution clé en main, adaptée à vos besoins grâce à une gamme modulaire d’équipements et de logiciels.
DIC :
La Corrélation d’Images Numériques est une technique optique sans contact qui permet de mesurer les déplacements et déformations sur la surface d’un matériau à partir d’images prises pendant une sollicitation. Aujourd’hui les logiciels les plus performants permettent une comparaison d’analyse successives en temps réel sans avoir à manipuler l’éprouvette. Le DIC apporte une innovation par rapport aux méthodes classiques, en offrant plus d’information, plus de précision, et une plus grande flexibilité.
Le choix du logiciel Mercury RT pour vos analyses DIC :
Le logiciel Mercury RT® permet d’analyser précisément la déformation des matériaux grâce à une grande diversité de paramètres, comme les déplacements, les souches principales, les taux de déformation et l’écart type.
Grâce à ses outils avancés, il devient possible de comparer les résultats expérimentaux aux simulations numériques, facilitant l’interprétation des comportements mécaniques.
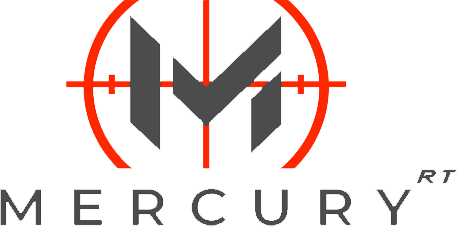
Exemples de paramètres disponibles :
Éléments d’analyse | Contenu |
---|---|
Déplacements | Déplacement global |
Déplacement en X (mm) | Déplacement X |
Déplacement en Y (mm) | Déplacement Y |
Filtre E1 | Souche principale maximale |
Filtre E2 | Souche principale minimale |
Souche EXX | Souche selon l’axe X |
Filtre EYY | Souche selon l’axe Y |
Tendance de cisaillement | Détection de zones de cisaillement |
Filtre E1 Taux (/s) | Taux de déformation principal maximal |
Filtre E2 Taux (/s) | Taux de déformation principal minimal |
Écart type (mm) | Écart type global |
Écart type X (mm) | Écart type sur l’axe X |
Écart type Y (mm) | Écart type sur l’axe Y |
Le logiciel Mercury RT permet un large choix de paramétrage de sondes :
Mercury RT® utilise des sondes virtuelles (points de repère sur l’image) pour mesurer la déformation et le mouvement des spécimens avec une grande précision. Il propose une variété de fonctions pour disposer ces sondes : simple distance entre deux points, répartition suivant la loi de Poisson, répartition courbée ou encore jauge de contrainte virtuelle.
Mesure en temps réel
Les capacités de mesure en temps réel de Mercure sont un outil puissant pour capturer et analyser le comportement dynamique des objets et des matériaux en temps réel. Cette fonction est particulièrement adaptée au test de résistance des matériaux, l’analyse des vibrations des structures et les tests de qualité des produits, ainsi que les pré-tests pour confirmer la corrélation avant le test.
Excellente interface utilisateur
Mercury RT® dispose d’un algorithme d’analyse de haute qualité ainsi qu’une excellente interface utilisateur. Il est possible de définir des conditions d’analyse détaillées et de confirmer visuellement les données par des vidéos et des graphiques en temps réel. Il est possible d’enregistrer les graphiques et vidéos sous forme de fichiers csv.
Essais sur matériaux
Extensomètre vidéo 2D/3D (VEX)
Mesure d’extension et de contraction (longitudinale, transversale)
Sonde à chaîne pour la mesure d’armatures
Outil de détection du rétrécissement au col
Jauge de déformation virtuelle
Mesure par motifs naturels
Mesure à haute température
Mesure de la propagation des fissures
Comptage de cycles dans les essais de fatigue
Essais sur composants
Mesure statique, quasi-statique et dynamique
Mesure de la distribution de déformation sur toute la surface
Caméra ultra-rapide intégrée
Mesure ponctuelle et surfacique du mouvement
Synchronisation de l’échantillonnage avec les événements dynamiques et périodiques
Analyse cinématique
API pour la communication et le contrôle E/S personnalisés
Mesure en chambre de pression
Mesure thermomécanique
Intégration de caméra thermique
Analyse et évaluation de la courbe limite de formage (FLC)
Analyse de gonflement (métaux en feuille, caoutchouc)
Pourquoi choisir le DIC ?
- Sans contact : pas besoin de jauge ou d’extensomètre collé.
- Pleine surface : mesure sur toute la zone d’intérêt, pas seulement en quelques points.
- Haute précision : détection de déplacements à l’échelle du micron. Précision sub-pixel (jusqu’à 0,01 pixel), grâce aux algorithmes de corrélation, souvent basés sur la FFT (Fast Fourier Transform).
- Polyvalent : s’adapte à tous types de matériaux et formes.
- Visualisation directe : identification claire des zones critiques (fissures, concentrations de contrainte).
Principales applications :
L’une des applications les plus répandues du DIC est l’essai de traction, où il permet de mesurer précisément l’allongement de l’éprouvette et d’identifier la localisation des déformations plastiques ou l’amorçage de fissures. Mais son utilisation ne s’arrête pas là :
- Essais de traction (tensil test) : suivi précis de l’allongement et de la localisation de la rupture.
- Fatigue, fluage (creep test), impact : analyse de l’évolution des déformations dans le temps.
- Validation de modèles numériques : comparaison directe avec les résultats expérimentaux.
- Contrôle qualité : inspection rapide et non destructive. Essais de traction : mesure précise des champs de déformation.
- Analyse 3D (stéréo-corrélation) : pour des pièces en volume ou à géométrie complexe.
- Vibro-DIC : corrélation d’images à haute fréquence pour la dynamique et l’analyse modale.
- Thermo-mécanique : couplage possible avec caméras infrarouges.
2D ou 3D ?
L’analyse peut être réalisée en 2D ou en 3D.
La 2D est adaptée aux surfaces planes ou lorsque la caméra est perpendiculaire au plan de mesure. La 3D, quant à elle, permet de capturer les déformations sur des géométries complexes ou non planes, en combinant les images de deux caméras synchronisées. Cela permet une reconstitution plus fidèle des déplacements et contraintes dans l’espace.
Analyse 2D
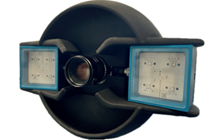
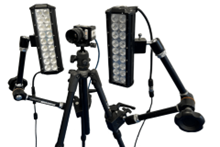
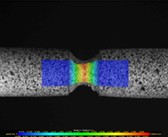
Analyse 3D
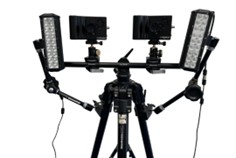
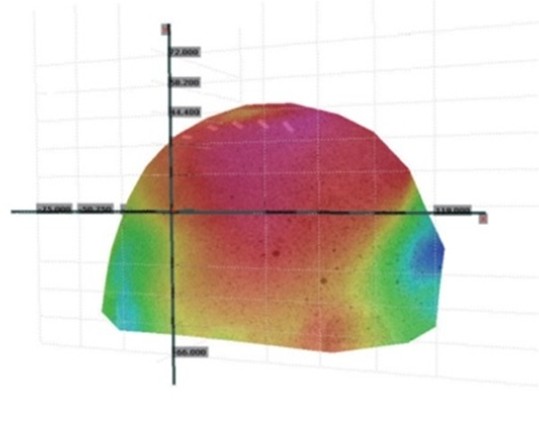